
“I
can still remember 30, 35 years ago when we used to tarpaulin-sided trailers cooled with dry ice to carry margarine”. Sebastian Uhlhorn, the man with these memories, is just 41 years old. But, as a fifth-generation representative of the logistics company Uhlhorn in Twistringen, Lower Saxony, he grew up with such stories – stories from the transport industry that sound a bit like something from a long-lost time. It was only a few years later that the technical quantum leap from dry ice to modern refrigeration units on the truck trailers followed.Mobile phones and navigation systems did not exist at the beginning of the 1990s either, of course. “When the drivers left on Sunday evenings, they called from the client on Wednesdays to let them know they were empty. Today, everything can be tracked online – even the temperature at which the vehicles cruise at on the road,” says the junior manager of Uhlhorn, explaining the turnaround in truck logistics.
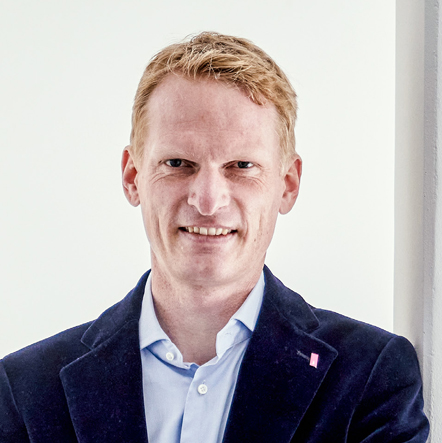
“The usability is easy, the reliability is great.”
Sebastian Uhlhorn
The temperature-controlled transport operations he is talking about present their own unique challenges. Fresh goods such as fish, meat, chocolate or vegetables have to be transported over long distances under the strict maintenance of the cold chain, and with the pressure to meet the set deadline. 200 refrigerated vehicles are on the road for Uhlhorn in Germany and Europe, with temperatures ranging from plus 30 to minus 25 degrees Celsius. “We run a lot at room temperature of around 18 degrees, for example, for chocolate products,” Sebastian Uhlhorn reports during the interview at the company headquarters. The view from the meeting room leads to the local railway station, and a large photo of the port of Hamburg hangs on the wall. Other logistics worlds in their own right.

Cooperation with Krone and Liebherr
In order to offer its customers a service with even more safety and reliability in the field of refrigerated logistics, Uhlhorn has been using the new “Celsineo” refrigeration system for about two years. It was developed by Krone, a long-standing partner of Uhlhorn, in cooperation with Liebherr, a company specialising in cooling technology and air conditioning. While normal refrigeration units have only one refrigeration circuit, in the Celsineo system, the cooling capacity is distributed over three plug-and-play refrigeration modules. Each of the three units has a self-sufficient control circuit. Thanks to this modular system, if one of the units fails, another one takes over its function and the cold chain is maintained. “In the event of any damage, you can complete the route and then carry out the repair at your leisure,” explains Sebastian Uhlhorn.
PROFILE
The Uhlhorn company was founded in 1876 as an agricultural trading company. Sebastian Uhlhorn’s grandfather then developed the company into a freight forwarding business in its third generation. Today, Uhlhorn Logistik has 850 employees, 500 to 550 of whom are drivers. The 420 tractor units and 500 semi-trailers in the company’s own fleet include around 800 scheduled vehicles. Uhlhorn has 92,200 square metres of warehouse space. In addition to food, the Twistringen-based freight forwarder, which operates from seven other major locations in Germany, transports paper and cardboard packaging, as well as building materials.
So far, the major freight forwarder from Lower Saxony has equipped one trailer with the Celsineo system, which transports fresh fish on the route between Hamburg and Berlin. Ten more refrigeration units of this brand are to be added in the course of the year. “Before we started using the new unit, we had a reserve trailer with which we could react quickly if the cooling system ever failed,” says Markus Rathje, branch manager at Uhlhorn Logistik in Hamburg. Sebastian Uhlhorn estimates that there are about five such failures a year. If there is a defect in the refrigeration of fresh produce, “then you immediately get alerted in scheduling, especially since many trucks run at night”. With fresh produce, in particular, there is only one deadline for delivery, as it is only briefly handled at the customer’s premises and then goes directly to the sales counters. In such a case of damage, the drivers have to head for the nearest workshop and possibly reload at the nearest refrigerated warehouse.
“This is time-consuming, labour-intensive and costly – not to mention nerve-wracking,” emphasises company boss Uhlhorn. “Being able to sleep peacefully again is actually the biggest perceived benefit of the new cooling system for us”.
“This is time-consuming, labour-intensive and costly – not to mention nerve-wracking,” emphasises company boss Uhlhorn. “Being able to sleep peacefully again is actually the biggest perceived benefit of the new cooling system for us”.
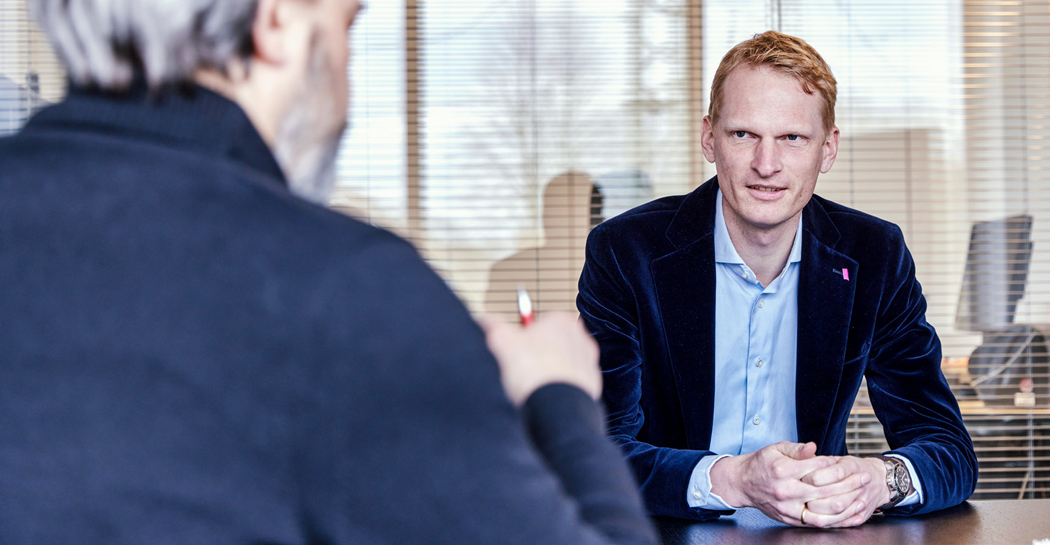
Intuitive and fast operability
“The modular solution is the first truly new approach to refrigeration logistics in decades – a real milestone. For me, this was ultimately also a decisive aspect in terms of securing the cold chain,” says Sebastian Uhlhorn, who particularly appreciates the ease of use associated with the system. In view of the fact that different drivers travel with the trailer between Hamburg and Berlin, it is important that the cooling system can be operated intuitively and quickly. “It has to be self-explanatory,” affirms the managing director. Branch manager Rathje compares the system to a smartphone: “Actually, everyone can handle it.” After a short introduction by Liebherr, the Uhlhorn drivers were in the picture. “The system is very straightforward,” confirms driver Holger Plassa, who is on the road with the Celsineo. Even for smaller companies that do not have a refrigeration technician among their staff, the Celsineo system, with its relatively simple handling, should be of interest. “In times of a shortage of skilled workers, this can definitely be a decisive aspect,” says Sebastian Uhlhorn.
AT A GLANCE

All good things come in threes
on Krone TV:
Driver shortage due to Brexit and Corona in the public consciousness
The shortage of drivers, in particular, also poses great challenges for the Twistringen-based haulage company. Brexit was the first time that this problem was discussed in a broader public sphere, and it was intensified again by the Coronavirus pandemic. “Before that, hardly anyone had thought about logistics chains, i.e. how goods actually get to the shops and what is needed in the run-up to that point,” says Uhlhorn. He welcomes the new public awareness of this problem, and that it has become more visible that there are too few truck drivers in all european countries. Sebastian Uhlhorn believes that the profession of “driver” is generally underestimated. At the same time, this work entails a lot of responsibility. Added to this is the potential daily stress caused by traffic jams on the motorways, the limited parking spaces and the sometimes poor treatment at the loading and unloading points. “That doesn’t make this job any easier,” adds the Twistringen haulage boss. At least in refrigerated logistics, the Celsineo system could eliminate at least one stress factor for drivers and dispatchers, because there have been no failures in the cold chain since the new technology was introduced at Uhlhorn Logistik.
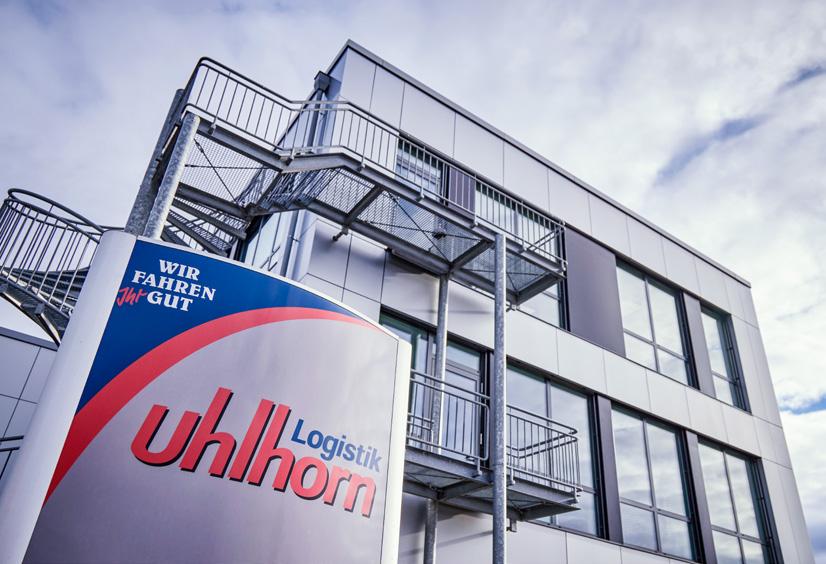
Photos: Martin Bockhacker, Krone TV