
“T
he pandemic is unique, no one could have foreseen an event of such magnitude,” says Dr Steffen Wagner, Head of Transport & Leisure at KPMG AG. Even if you had tried to prepare for it: Since all sectors were really affected, there would have been no easy solution. Shortages of raw materials, limited supply capacities, an intensified shortage of skilled workers, increased effort due to hygiene requirements and comprehensive border controls – entrepreneurs have had to overcome all kinds of challenges since the beginning of 2020. According to Steffen Wagner, Covid-19 has increased the already high dependence of supply chains on factors such as raw material shortages: “We have seen how even small changes in the transport chain can lead to its collapse – especially in the automotive industry, where a tightly synchronised supply chain with just-in-time delivery to the assembly line is common today.”DR STEFFEN WAGNER
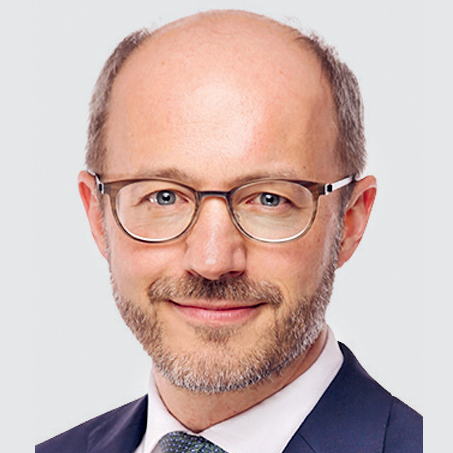
Head of Transport
and Logistics, KPMG
Dr Steffen Wagner has been an analyst at KPMG since 1997 and became a partner in the Corporate Finance/M&A division in 2004. He holds a lectureship at the Chair of Accounting & Capital Markets at the University of Mannheim.
The term “whip effect” applies here, which describes a scenario where even small fluctuations in demand can lead to significantly larger movements even far down the supply chain, i.e. like the small movement of a hand that can make a whip crack: “When there was suddenly so much demand for toilet paper in the first lockdown, it caused big problems elsewhere in the supply chain.”
AUTOMOBILE MANUFACTURERS WERE LEFT HIGH AND DRY
There was always enough toilet paper – it just had to be brought to the shops faster in the required quantity. Raw materials such as wood or steel, on the other hand, became seriously scarce because they were in greater demand: In the case of wood, for example, the private construction boom in the USA fuelled sales, while North America – the traditional source of wood there – was no longer able to deliver because many forest fires had severely reduced the stock. Rising demand from China also drove up timber prices. Wood was increasingly bought from Europe, which was also felt by every private house builder in this country. This is because prices in the domestic market followed higher export prices and a sell-out of the European domestic market took place.
Furthermore, raw materials become scarce when they suddenly “migrate” heavily to other industries: “When semiconductor chips, which are mainly produced in Asia, were much less in demand by the automotive industry in the mid-2020s, they flowed instead into consumer electronics, which boomed during the pandemic,” says Steffen Wagner. “Car production ramped up again in the second half of the year – but remains stranded for the time being in terms of chips because now there was a shortage of supply for them.” So there can be changes on the supply side as well as the demand side – and the effects can be significant.
Furthermore, raw materials become scarce when they suddenly “migrate” heavily to other industries: “When semiconductor chips, which are mainly produced in Asia, were much less in demand by the automotive industry in the mid-2020s, they flowed instead into consumer electronics, which boomed during the pandemic,” says Steffen Wagner. “Car production ramped up again in the second half of the year – but remains stranded for the time being in terms of chips because now there was a shortage of supply for them.” So there can be changes on the supply side as well as the demand side – and the effects can be significant.
GEORG SASSE
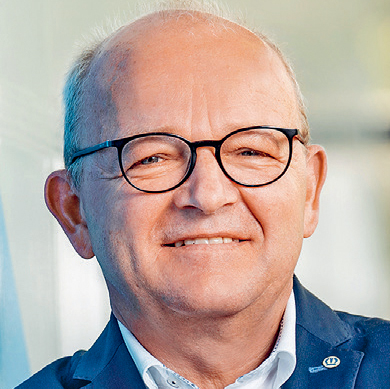
Head of Strategic
Purchasing Krone Holding
Georg Sasse completed his apprenticeship at Krone back in 1984. After his further training as a technical business economist, he went into purchasing – first in Werlte, then in Spelle and since 2020 in the holding company.
As Purchasing Manager of Krone Holding, Georg Sasse and his team are continuously faced with the challenge of ordering at competitive prices and getting the material to the right place at the right time in the necessary quality. In the Coronavirus pandemic, this is anything but easy. “Currently, there is no commodity group in the materials we process where the supply is relaxed,” he explains. In his 20 years as Head of Purchasing in the company, he has never experienced a situation like the current one: “But I still see it positively and remain optimistic. Krone has a strong foundation and long-standing supplier relationships that we can build on. Any entrepreneur will only stay in the market if he or she offers competitive prices. As a trailer manufacturer, we have proven over the past year that we can rise to this challenge together with our suppliers.”
RELATIONSHIPS WITH SUPPLIERS ROOTED IN TRUST
Ensuring competitiveness – This is the task facing all players in the transport industry. “Our most important task is to secure this for the future.” In order to be able to react flexibly and quickly to different market situations with the supplier structure, continuous and transparent cooperation is required. Krone always stays in touch with its partners and maintains open communication.
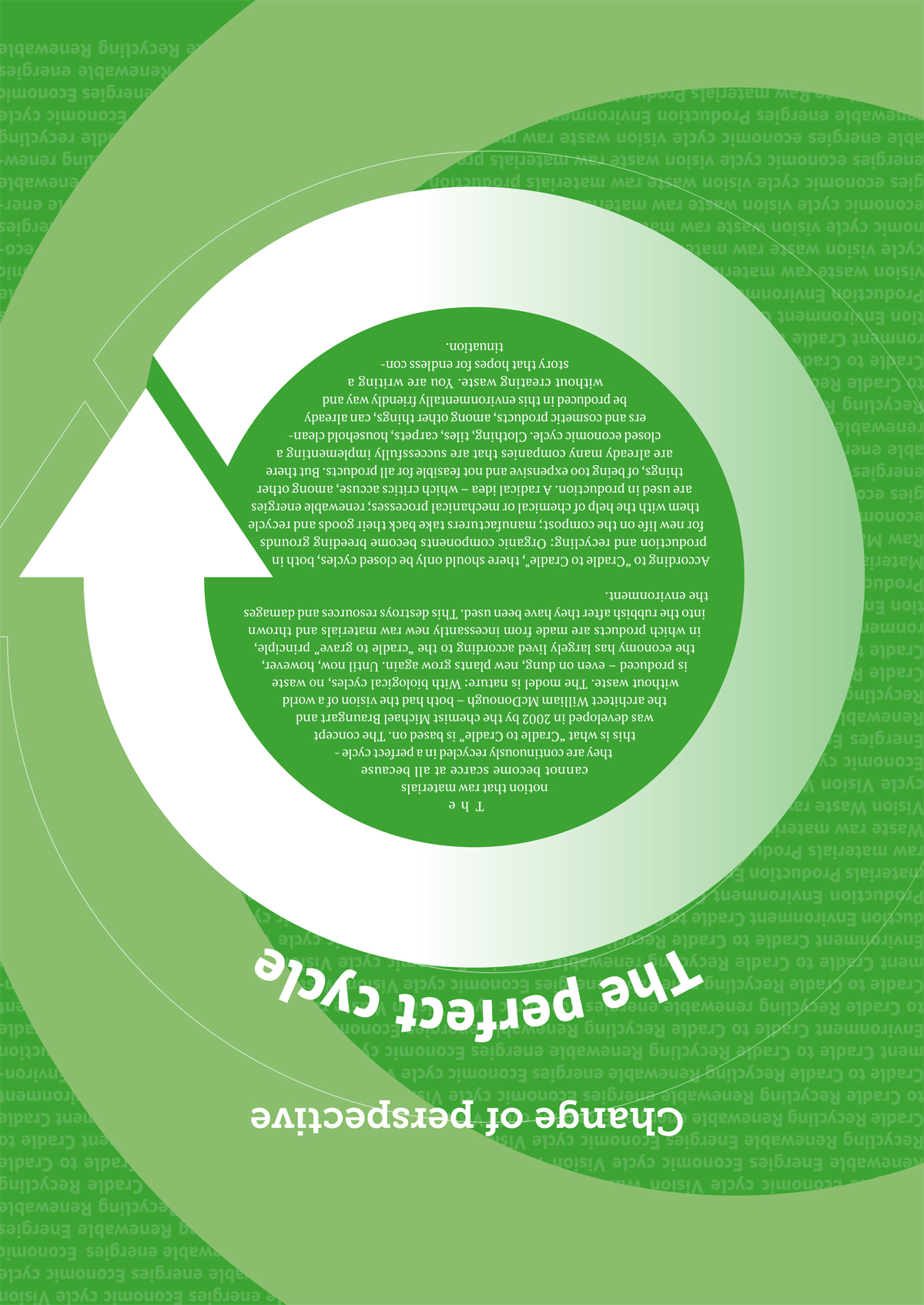
Facts & Figures
76 %
of the disruptions in the supply chains are due to a lack of containers. (DIHK)
ONLY 50 %
of container ships were on time in November 2020. On average, ships arrived 5.1 days late. (Sea Intelligence)
64 %
of companies are looking for new or additional suppliers due to raw material shortages and supply bottlenecks. (DIHK)
AROUND 5 MILLION VEHICLES
Production in 2021 will be lower due to the shortage of semiconductors in the automotive industry. (Automotive Research)
25 BILLION EUROS
is the amount that bottlenecks and delays in global supply chains cost the German economy. (estimate by the Kiel Institute for the World economy 2021)
During the pandemic, in addition to the shifts between supply and demand, there were also instances of collapse in transport capacities – again, for very different reasons: In air cargo, passenger aircraft – which previously accounted for about 50 per cent of international capacity – went missing. The transporters could hardly counter this rapid, substantial and so sudden shortage. Volumes shifted from air freight to sea freight – but trans-shipment soon stopped working in the ports due to hygiene regulations, a lack of containers and a shortage of staff. “The ships were anchored in the harbours, the crews were stuck there,” as Steffen Wagner explains. The traffic jam in the Suez Canal in March 2021 was another influencing factor; and international land transport was slowed down by entry stops, among other things.
TWO EFFECTS AT THE SAME TIME
“The fact that supply chains are massively disrupted has happened more often in the past, for example, during the oil crisis in the 1970s or the eruption of the Icelandic volcano Eyjafjallajökull in 2010. In the Covid-19 pandemic, however, the situation was not localised but affected the entire world. It occurred in a very condensed way and everything happened in a short space of time.” The interconnectedness and fragility of the supply chains already existed before, due to the international dependencies in the global economy, says Mr Wagner, himself a logistics expert: “For example, the EU imports almost all the rare earths it needs in production from China. But the Coronavirus had now triggered two parallel effects: on the one hand, shifts in demand structures and, on the other, the loss of transport capacities.”
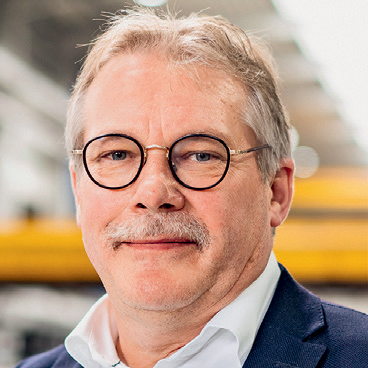
“The current price developments and material availability in the market are very challenging. However, Krone continues to be a reliable partner for all customers. We are working flat out every day to keep our promises. So far, we have achieved this; also, when compared to the competition, we have been very successful.”
Bernhard Brüggen, CEO
Of course, such a huge crisis on this scale could not have been foreseen. But what can be learned from it? Steffen Wagner expects companies to spend a lot of time and energy on organising their supply chains to be even more transparent and thus more predictable: “The aspect of transparency in the supply chain will become much more important.” This is accompanied by a new risk management approach for calculating costs, which also has an impact on the area of transport and supply chain costs: “In the pandemic, we saw that when in doubt, it can be cheaper to keep larger stocks on hand.” Relevant data is again needed for planning such precautionary measures. “The importance of interlinking supply chains, data exchange and platform economy will thus continue to grow,” says Wagner.
FOCUS ON RISK MANAGEMENT AND FLEXIBILITY
Once a year, the consulting firm KPMG asks managers in German companies across all sectors which topics they are prioritising for the coming twelve months: “The transport industry had, for a long while, put its main focus on digitisation and the shortage of skilled workers until suddenly, in 2020, the factors of risk management and flexibility were mentioned most often.” Nevertheless, according to Steffen Wagner, digitisation remains a very important keyword: “Companies today are driven by data analytics. But many companies do not yet have the necessary technical basis for this. For them, digitisation, therefore, means above all modernising, i.e. adapting their systems to the latest technological standards. Provisions are already being made: New production facilities for chips have been established in Germany. Such measures to safeguard production will increasingly exist in this country. But global dependencies will continue. Companies have to reckon with this risk – and live with it.”
Illustrations: iStock/Victor_85, iStock/Iuliia Kanivets Photos: KPMG, Krone